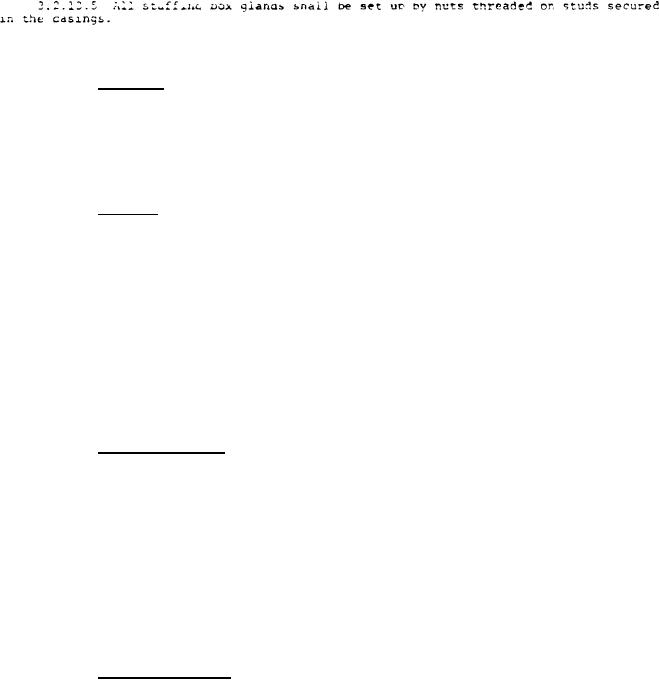
MIL-P-24475 (SHIPS)
3.2,13.3 The design shall insure that positive liquid pressure is supplied to the
seal faces under all conditions of operation , and that there is adequate circulation of
the liquid at the seal faces to minimize the deposit of foreign matter on the seal parts.
The pump certification data shall contain certification by the seal manufacturer that there
will be adequate circulation of liquid and adequate lubrication at the seal faces when the
seal is installed as shown on the drawing.
3. 2.13.4 Mechanical shaft seals shall be positioned on the shaft by means of stub or
step sleeves. Mechanical shaft seals shall not be positioned by use of set screws alone.
3. 2.13.6 Space shall be provided between bearings and stuffing boxes to permit easy
inspection and overhaul of bearings and shaft seals.
3.2.14 Couplings.
3.2.14.1 For horizontal or vertical units requiring couplings, an all-metal flexible
coupling shall be installedc between the pumps and driving units. Nonmetallic couplings
may be used when specified in the contract or order.
3.2.14.2 All flexible coupling pump hubs shall be keyed to the shafts and secured
by lock nuts. For pump shafts one inch in diameter and larger, the hubs shall be fitted
on a taper with keys.
Fittings .
3.2.15
3.2.15.1 All horizontal and vertical pump casings shall be fitted with drain connections
in accordance with MS16142 and MS18229 to permit the complete drainage of the pumps without
disassembly of the pump.
3.2.15.2 The bottom of all drip pockets, if utilized, shall be tapped for drain
connections.
3.2.15.3 All pumps shall be fitted with vent connections to prevent entrapment of air
or vapor which would adversely affect the operation of the pump. Special attention should
be paid to vent location so that the seal lubrication requirements of 3.2.13.3 are met during
pump start up and operation.
3.2 .15.4 Pump discharge shall be provided with gage boss. Pressure gages when provided
with the units shall be mounted in accordance with Drawing 810-1385850. Gages shall be
positioned for accessibility for reading and maintenance. Gages shall be secured on the
parent equipment in such a manner as to prevent vibration, breakage and disconnection.
3.2.16 Rotating assembly.
3.2.16.1 All rotors shall be dynamically balanced with all rotating parts connected
thereto; for common shaft assemblies this requires dynamic balance with the rotating elements
of the driving unit in place. However, rotating parts may be balanced individually provided
that when assembled the unbalance shall not exceed the limits specified in MIL-STD-167.
3.2.16.1.1 Where balancing is required as a maintenance procedure to maintain proper
vibration or noise performance of the pump and driver unit in service, the pump shall be
designed such that balancing may readily be performed by overhaul activity personnel.
3.2.16.1.2 The pump design shall be such and calculations shall be made to demonstrate
that the maximum operating speed of the pumps will be not greater than 70 percent of the
first critical speed.
3.2.16.2 Motor driven pumps shall be capable of reverse rotation for a period of 1
minute at maximum rated revolutions per minute (r.p.m. ) without damage.
3.2.17 Threaded fasteners. Threaded parts such as bolts, studs and nuts shall conform
to Handbook H28. The setting end of studs shall be class 5 fit or class 3 fit with lock-
ing resin in accordance with MIL-S-22473. The nut end shall be class 3 fit.
7
For Parts Inquires call Parts Hangar, Inc (727) 493-0744
© Copyright 2015 Integrated Publishing, Inc.
A Service Disabled Veteran Owned Small Business