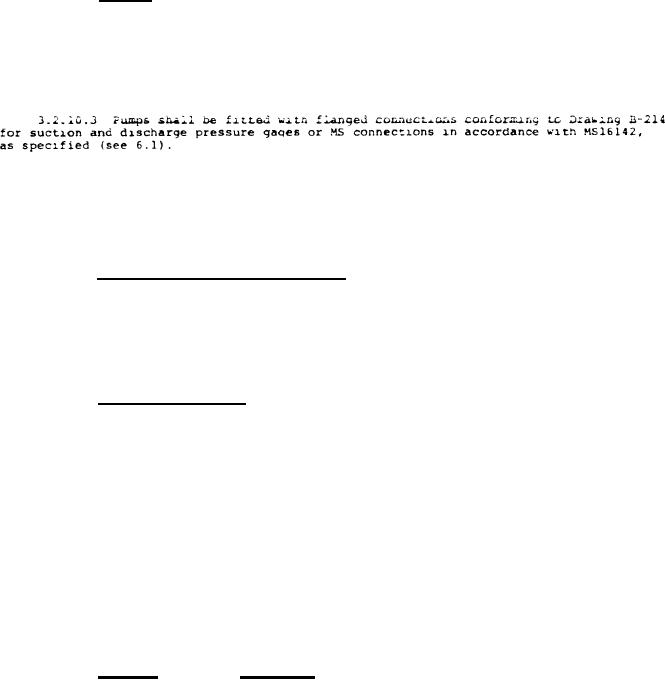
MIL-P-24475(SHIPS)
3.2.10 Casings.
3.2.10.1 The design of all flexible coupled pumps is to be such that the complete
rotating element may be removed without disturbing the suction and discharge piping. All
close-coupled and rigid-coupled pumps shall be designed to permit ready replacement of
wearing parts.
3.2.10.2 Clearance shall be provided around bolt heads and nuts to permit the use of
ordinary tools.
3.2.10.4 Casing fittings shall be as specified in 3.2.15.
3.2.10.5 Gasket compression and tolerances shall not affect bearing, bushing and
wearing ring fits to an extent that will adversely affect reliability and performance.
3.2. 10.6 Casing thickness shall include an allowance for corrosion and the possibility
of core shift.
3.2.11 Suction and discharge connections.
3.2.11.1
Suction and discharge connections shall be flanged for mating with flanges
in accordance
with MIL-STD-43B or MIL-STD-777 as applicable and as specified (see 6.1) .
The thickness
of the flanges shall be not less than that specified in the applicable
specification
or drawing.
3.2.11.2
Suction and discharge connections shall be located on the bottom or fixed
half of casings except on close-coupled pumps.
3.2.12
Impellers and shafts.
3.2.12.1
Outside surface of impellers shall be smooth finished
3.2.12.2 Impellers shall be keyed on the shaft and securely held against lateral
movement by locked nuts.
3.2.12.3 Impellers shall not be furnished with wearing rings. The repeller hub wear-
ing surfaces shall have material thickness to permit reducing the diameter of the impeller
hubs by as much as 0.050 inch to accommodate undersize casing wearing rings to restore
design running clearance (if required) .
3.2.12.4 All shaft threading, except threading for rolling contact bearing locknuts,
shall be counter to the direction of rotation. Shaft threading for rolling contact bearing
locknuts may be clockwise or counterclockwise.
3.2.12.5 The shafts of close-coupled pumps shall be of one piece construction.
3.2.12.6 Shaft flingers shall be provided adjacent to stuffing boxes for all pumps.
The flinger shall be so located that leakage which might occur between the stuffing box
is not allowed to reach pump or motor ball bearings.
3.2.13 Stuffing boxes and mechanical shaft seals.
3.2.13.1 All pumps shall be provided with mechanical shaft seals. The gland of each
seal, which shall be of solid construction, shall be designed to incorporate two or more
rings of packing for use in the event of a mechanical shaft seal failure. Seal intervals
shall be constructed of nickel-copper alloy. The stationary sealing face shall be constructed
of tungsten carbide. The rotating sealing face shall be constructed of tungsten carbide or
carbon.
3.2.13.2 The mechanical shaft seal shall be lubricated from a separate salt or fresh
water source. A cyclone separator shall be provided if a salt water source is used, to
clean the water source. A double shaft seal assembly may also be used, incorporating a
pressurized, dead-ended lubrication space. The liquid being pumped may not be used to
lubricate the shaft seal.
6
For Parts Inquires call Parts Hangar, Inc (727) 493-0744
© Copyright 2015 Integrated Publishing, Inc.
A Service Disabled Veteran Owned Small Business