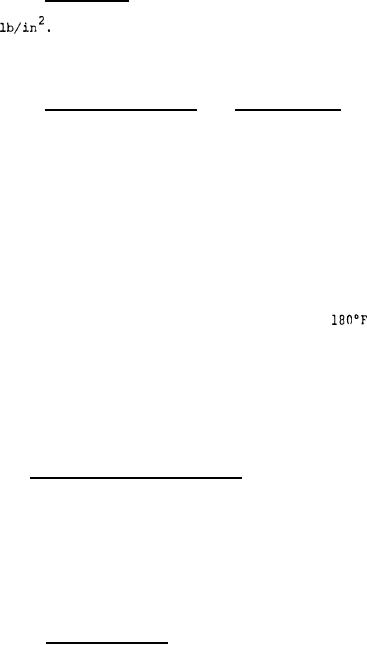
MIL-P-18526A(SH)
(b) Mechanical soundness and capacity tests (see 4.4.1.2).
(c) Noise test (to be performed only when specified) (see 4.4.1.3).
4,4.1.1 Hydrostatic ressure test. Each pump casing shall be tested hydrostatically
to a pressure one and one-half times the maximum discharge gage pressure but in no case less
Hydrostatic test shall be maintained for at least 30 minutes or longer as
than 50
necessary for examination of entire casing.
Acceptance criteria:
Pumps shall exhibit no leakage through the casing material
or joints,
4.4.1.2 Mechanical soundness and capacity tests . This shop test shall be conducted,
recorded, and reported in accordance with the rotary pump Pating Standard and Test Code of
the Hydraulic Institute, to the extent that these standards are applicable and are not in
conflict with the requirements specified herein. The test record for each pump shall identify
the pump by manufacturer's serial and model numbers, i.e., it shall indicate pump size of
internals governing capacity and pressure being tested in the pump, it shall include a
description (by legend. and sketch) of the test stand arrangement including an identifying
list of test instruments used and the data when last calibrated, and it shall include the
data sheets of all recorded data and sample calculations of data conversion to specified
conditions . The test shall be performed as follows: Operate the pump, and its driver if
motor driven, continuously for at least 30 minutes, to verify the ability of the pump to
operate in conformance with contract requirements. Pumps shall be tested to determine their
ability to deliver rated capacity using the specified fuel . This is to be performed against
rated discharge pressure with the minimum specified suction lift.
Acceptance criteria:
Oil temperature rise in force-feed lubricated bearings shall
not exceed 50°F in any bearing and shall not exceed a maxi-
mum temperature of
and the criteria specified in
4.4.3.4 (b), (c), and (d).
4.4.1.3 Noise test. When specified (see 6.2.1), a noise test shall be conducted and
reported in accordance with MIL-STD-740 (see 3.3.3.5) . The noise test stand details,
instrumentation, and testing technique shall be submitted by the contractor for review by
the procuring agency prior to test commencement. Noise tests shall be performed with the
driver furnished with the pump. Airborne noise tests shall be conducted on the lead unit
only on each contract or order.
Acceptance criteria:
Unit shall meet the noise level limits specified (see 6.2.1).
4.4.2 Performance evaluation tests. one pump of each class, design, and size on each
contract or order, shall successfully undergo the performance evaluation tests to establish
the complete pump performance map and to ascertain compliance with the specified performance
requirements . A substitute driver may be used for turbine driven pumps. When pumps of
identical design and size are being produced under two or more contracts within a two year
period. only one series of performance evaluation tests shall be required for that produc-
tion run. The proposed test procedures for the performance evaluation tests shall be sub-
mitted to the procuring agency approximately at the time of drawing submittal. The following
tests shall comprise the performance evaluation tests:
(a)
performance test (see 4.4.2.1).
Packing/seal and alinement procedure test (see 4.4.2.2) .
(b)
4.4.2.1 Performance test. Each test pump shall be operated initially to determine pump
characteristics with each of the following fuels: DFM and JP-5. Pump shall be operated
with rated discharge pressure, suction temperature, and specified suction lift held constant,
and flow varied from rated to minimum flow in discrete intervals (not less than 5) to devel-
op characteristic curves for each fuel. Pump shall be operated a minimum of 1/2 hour at
each test point to collect data after all parameters have stabilized. Data collected shall
be used for compilation of the pump performance map and shall include efficiency and horse-
power curves.
Each test pump shall meet rated conditions with a flow ca-
Acceptance criteria:
pacity tolerance of plus 10 percent minus 10 percent.
16
For Parts Inquires call Parts Hangar, Inc (727) 493-0744
© Copyright 2015 Integrated Publishing, Inc.
A Service Disabled Veteran Owned Small Business