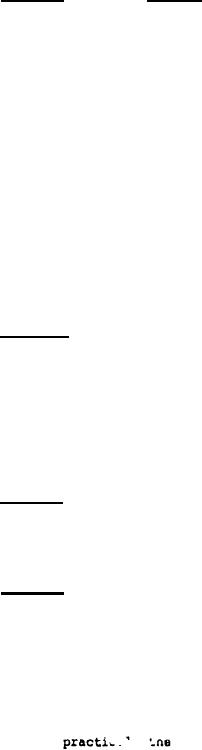
MIL-P-17945A(SH)
3.2.14.4 Shaft threading shall be counter to the direction of rotation except where
both right hand and left hand units of the same design are involved; in which case, in order
to reduce the number of shafts required for repair parts, the threading shall be right hand
for all units and the threaded parts shall be locked in place.
3.2.14.5 Shaft flingers shall be provided adjacent to stuffing boxes for all pumps.
3.2.14.6 Shafts of d.c. motor driven pumps shall be provided with means to permit the
ready and direct use of portable tachometers.
3.2.15 Stuffing boxes and packing.
3.2.15.1 Pumps shall be provided with mechanical shaft seals. Pumps for salt water
service shall also be fitted with cyclone separators (see 6.2.1) . Cyclone separators shall
be constructed of nickel-copper alloy. The gland of each seal shall incorporate two or more
rings of packing for use in the event of a mechanical seal failure, Seal internals for sea
water service pumps shall be constructed of nickel-copper alloy. -Seal internals for fresh
water service pumps shall be constructed of 304 or 316 corrosion-resistant steel or Ni-Cu
alloy. The mechanical shaft seal shall have a tungsten carbide against carbon sealing surface.
Fittings for abrasive separators and pump casings shall be of the straight thread type with
O-ring seals and shall be constructed of nickel-copper alloy. Tubing shall be copper-nickel
(70-30) In accordance with MIL-T-16420.
3.2.15.2 Mechanical shaft seals shall be positioned on the shaft by means of stub or
step sleeves. Mechanical shaft seals shall not be positioned by use of set screws alone.
3.2.15.3 Positive liquid pressure shall be supplied to the seal faces under all condi-
tions of oprration and adequate circulation of the liquid at the seal faces shall be provided
to minimize the deposit of foreign matter on the seal parts.
3.2.15.4 Stuffing box glands shall be set up by nuts threaded on studs secured in the
casings.
3.2.15.5 Space shall be provided between bearings and stuffing boxes to permit easy
inspection of mechanical seals and bearings.
3.2.16 Couplings.
3.2.16.1 Flexible-couplings shall be of all-metal construction.
3.2.16.2 Flexible-coupling hubs shall be keyed to the shafts. For shafts 3/4 inch and
smaller, the coupling hubs shall be secured to the shafts by lock nuts or set screws. For
shafts larger than 3/4 inch, the coupling hub shall be secured to the shafts by lock nuts.
For shafts 1 inch in diameter and larger, the hubs shall be fitted on a taper with keys
parallel to the taper.
3.2.16.3 Flexibly-coupled units shall have coupling guards.
Guards shall permit ready
access to the coupling for lubrication and inspection.
3.2.17 Fittings,
3.2.17.1 The bottom of all pump casings shall be fitted with drain connections to
permit complete draining of the pumps without disassembly of the pumps.
3.2.17.2 The bottom of drip pockets shall be pipe tapped for drain connections.
3.2.18 Painting.
3.2.18.1 All external unmachined surfaces that are not inherently corrosion-resistant
a s defined in MIL-E-917 shallall be processeed (treaed, plated, or painted) in accordance with
MIL-E-917 to provide corrosion-resistnace. Paint shall not be applied to any internal
machined surfaces. When desired, (for convenience or appearance) contiguous non-ferrous
surfaces may also be painted.
3.2.19 Threaded parts such as bolts, studs, and nuts shall conform to Handbook H28.
3.2.20 Welding shall be in accordance with MIL-STD-278.
3,2.20.1 Where
use of silver-brazed joints shall be avoided. Where
used silver-brazed joints shall conform to the fabrication and inspection requirements of
NAVSEA 0900-LP-001-7000.
6
For Parts Inquires call Parts Hangar, Inc (727) 493-0744
© Copyright 2015 Integrated Publishing, Inc.
A Service Disabled Veteran Owned Small Business